Урок №1 Перевірка маркування і
якості зварювальних електродів для повітряно-дугового
різання,дроту,флюсів,захисних газів.
Види контролю якості
Залежно від характеру дії на матеріал зразка або виробу всі різноманітні методи контролю якості зварних з'єднань можуть бути поділені на дві основні групи: методи контролю без руйнування зразків або виробів — неруйнівний контроль і методи контролю з руйнуванням зразків або виробничих стиків — руйнівний контроль.
Всі види неруйнівного контролю класифікуються за наступними основними ознаками:
—за характером фізичних полів або випромінювань;
—за характером взаємодії фізичних полів або речовин з контро-льо ним об'єктом;
—за первинними інформативними параметрами, розглянутих методів контролю;
—за способами індикації первинної інформації;
—за способом представлення кінцевої інформації.
Всі методи неруйнівного контролю поділяються згідно зі стандартом на наступні види: акустичний, капілярний, магнітний, оптичний, радіаційний, радіохвильовий, тепловий, електричний, електромагнітний (вихрові струми), течошукач.
До неруйнівних видів контролю слід віднести і контроль зовнішнім оглядом та обмірюванням, який має суттєве значення для одержання якісних зварних конструкцій. До руйнівних видів контролю відносяться механічні випробування зварних з'єднань. Для оцінки механічних властивостей зварні з'єднання піддають різним випробуванням. Механічні випробування зварних з'єднань застосовують у тих випадках, коли потрібно визначити якість зварювальних матеріалів, розробити оптимальні технологічні режими (особливо при зварюванні спецсталей), і при перевірці кваліфікації зварників, чи при їх переатестації.
②
Візуальний контроль
Візуальний контроль матеріалу (напівфабрикатів, заготівель, деталей) і зварених з’єднань проводять на наступних стадіях:
- вхідного контролю;
- виготовлення деталей, складальних одиниць і виробів;
- підготовки деталей і складальних одиниць до складання;
- підготовки деталей і складальних одиниць до зварювання;
- складання деталей і складальних одиниць під зварювання;
- процесу зварювання;
- контролю готових зварних з’єднань;
- виправлення дефектних ділянок у матеріалі й зварених з’єднаннях;
- оцінка стану матеріалу й зварних з’єднань у процесі експлуатації зварних з’єднань в тому числі після закінчення встановленого строку їхньої експлуатації.
Візуальним оглядом перевіряють якість підготовки і складання заготівок під зварювання, якість виконання і якість готових зварних швів.
Візуальним оглядом конролюють всі зварні вироби незалежно від використання інших видів контролю.
Візуальний огляд в багатьох випадках достатньо інформативний, найбільш дешевий і оперативний метод контролю.
Контроль заготовки і складання.
Зовнішньому огляду піддають матеріал, який може бракуватися при наявності вм’ятин, окалин, слідів корозії і т.п. Визначають якість підготовки кромок під зварювання і складання заготовок: чистоту кромок, відповідність зазорів допустимих значень, правильність поділу кромок і т.п. Для цього можна використовувати спеціальні шаблони або універсальний інструмент.
Спостереження за процесом зварювання.
Візуально контролюють режим зварювання, газовий захист дуги, правильність положення валиків в багатошарових швах і т.п.
Часто контролер за допомогою лупи може перевірити перші шари шва, що дає можливість попередити в подальшій появі тріщин в шві і колошовній зоні. Якість окремих шарів перевіряють шляхом порівняння з еталоном.
Огляд готових з'єднань.
Перш за все зовнішнім оглядом неозброєним оком або в лупу перевіряють наявність тріщин, підрізів, свищів, пропалів, непроварів (кореня і кромок).
При візуальному контролі зварних з’єднань контрольована зона повинна містити в собі поверхню металу шва, а також зону основного металу, що примикає до нього в обидва боки від шва шириною:
- не менш 5 мм – для стикових з’єднань, виконаних дуговим і електронно-променевим зварюванням, зварюванням оплавленням при номінальній товщині зварних деталей до 5 мм включно;
- не менше номінальної товщини стінки деталі – для стикових з’єднань, виконаних дуговим і електронно-променевим зварюванням, зварюванням оплавленням при номінальній товщині зварних деталей понад 5 до 20 мм;
- не менш 20 мм – для стикових з’єднань, виконаних дуговим і електронно-променевим зварюванням, зварюванням оплавленням, при номінальній товщині зварених деталей понад 20 мм, а також для стикових і кутових з’єднань, виконаних газовим зварюванням, незалежно від номінальної товщини стінки зварених деталей і при ремонті дефектних ділянок у зварених з’єднаннях.
Зварні шви приймають за зовнішнім виглядом в порівнянні з еталонами. Геометричні параметри швів виміряють за допомогою шаблонів або вимірювальних інструментів.
ільки після зовнішнього огляду виробу з'єднання підлягають будь – яким фізичним методам контролю для визначення внутрішніх дефектів. Ретельний зовнішній огляд – звичайно дуже проста операція але може бути високоефективним засобом попередження і виявлення дефектів.
При візуальному контролі застосовують такі інструменти:
– лупи, у тому числі вимірювальні;
– лінійки вимірювальні металеві;
– косинці перевірочні 90 град. лекальні;
– штангенциркулі,
– щупи;
– кутоміри з ноніусом;
– мікрометри;
– калібри;
– ендоскопи;
– шаблони, у тому числі спеціальні й радіусні, різьбові й інші;
– перевірочні плити;
– штрихові міри довжини (сталеві вимірювальні лінійки, рулетки).
Допускається застосування інших засобів візуального й вимірювального контролю, при умові наявності відповідних інструкцій, методик їхнього застосування. Для виміру форми й розмірів крайок, зазорів, зібраних під зварювання деталей, а також розмірів 12 виконаних зварених сполук дозволяється застосовувати шаблони різних типів. Погрішність вимірів при вимірювальному контролі не повинна перевищувати величин, зазначених у робочих кресленнях.
③
Контроль зварювальних матеріалів.
Частина дефектів зварних швів виникає в результаті застосування недостатньо якісних вихідних матеріалів (основних і зварювальних), порушення вимог щодо складання під зварювання, технологію його виконання. Запобігти появі таких дефектів допомагає попередній і поопераційний контроль, який виконується методом зовнішнього огляду і перевіркою відповідності розмірів.
До вихідних матеріалів належить і основний метал, з якого збирають конструкції, зварювальні електроди, дроти, флюс і захисні гази.
У литих виробах, металопрокаті перевіряють наявність сертифікату, заводського маркування і відповідність їх проекту. Зовнішнім оглядом установлюють наявність раковин, розшарувань, тріщин, у трубі — якість скосу кромок, у заготовках із спецсталей — відповідність хімічного складу і механічним властивостям.
Зварювальні електроди піддають зовнішньому огляду з метою виявлення механічних пошкоджень покриття, відсутності корозії стрижня під ним, а також визначення товщини нанесеного покриття.
Покриття електродів діаметром до 4 мм і більше не повинне руйнуватися при вільному падінні електрода на гладку стальну плиту з висоти 1 м і 0,5 м відповідно. Можуть допускатися часткові відколи покриття до 5% довжини покритої частини електрода. Придатність електродів установлюють за результатами технологічної проби. При цьому визначають характер плавлення електронного стрижня й покриття, якість формування зварного шва, ступінь розбризкування, утворення «дашка», легкість відділення шлаку та ін. Оглядом поверхні шва визначають наявність пop, які виходять на поверхню, у зломі таврового шва — наявність пop і шлакових включень.
Зварювальний дріт перевіряють на чистоту поверхні від оксидів, іржі та забруднень. Якщо властивості дроту відповідають сертифікату й вимогам стандартів, то забруднення
на поверхні (але не оксидні) можуть бути очищені механічним чи хімічним способом.
Використання дроту з мідним покриттям виключає можливість утворення іржі й сприяє утворенню якісних зварних швів.
При необхідності виконується технологічна проба, за якою встановлюють якість формування зварного шва, ступінь розбризкування, легкість відділення шлаку, утворення пop, так як і при перевірці електродів.
Зварювальний флюс контролюють методом перевірки грануляції й технологічної проби, яка дозволяє, як і у випадку перевірки електродів і зварювального дроту, визначити за зовнішнім оглядом шва і його зламу якість формування, поро- і шлакоутворення, відділення шлаку. При зварюванні відповідальних конструкцій флюс перед роботою перевіряють на гранулоутворюючий склад, однорідність, насипну щільність і забрудненість. При вологості понад 0,1% флюс просушують.
Захисні гази (вуглекислий газ, аргон) при наявності сертифікатів заводу-виготівника піддають контролю тільки в тому випадку, коли у зварних швах, виконаних з їх використанням, виявляють недопустимі дефекти.
Зібрані під зварювання деталі перевіряють на відповідність вимогам технології та проекту. За допомогою спеціальних шаблонів і лінійок перевіряють якість зрізу кромок (рівномірність і величину кута розкриття, відсутність місцевих виривів), наявність і величину притуплення, перевищення кромок, величину й рівномірність зазору. Особливу увагу приділяють перевірці чистоти поверхонь кромок і зони, яка прилягає, зачищанню прихваток.
При зварюванні сталей (у т. ч. і тих, які гартуються) товщиною понад 20 мм поверхні прихваток старанно перевіряють на наявність тріщин.
Прихватки з тріщинами повинні бути старанно видалені, місця основного металу, де вони знаходилися, оглядають за допомогою лупи і тільки після цього виконують нові прихватки із застосуванням особливих технологічних прийомів, наприклад, підігріву.
Питання для самоконтролю.
1. Назвіть руйнівні методи контролю.
2. Назвіть неруйнівні методи контролю.
3. Чому методи контролю називаються «руйнівними»?
4. Як проконтролювати якість зварювальних електродів?
5. Як контролюють на якість зварювальний флюс?
6. Назвіть інструменти, які використовуються при візуальному контролі якості зварних Слайд 1Мал.1 Гарячі тріщини в зварних з’єднаннях: 1,2 – повздовжні, 3,4 – поперечні в шві та навколошовній зоні; 5 – поперечні тріщини по товщині зварювального металу Мал.2. Характер холодних тріщин Мал.3 Види дефектів у зварних з’єднаннях: а – наплив; б – підріз; в – непровар; г – зовнішні тріщини і пори; д – внутрішні тріщини і пори; е – внутрішній не провар; ж – шлакові включення Дефект – це відхилення від норм, передбачених стандартами і технічними умовами на зварні з’єднання
Слайд 2Дефекти форми і розмірів шва: а-неповномірність шва; б-нерівномірність ширини стикового шва; в-нерівномірність довжини катету кутового шва; h- необхідна висота та випуклість шва “Зовнішні дефекти”
Слайд 3Дефекти зварних з’єднань “Причини”
Слайд 5Загальні причини утворення дефектів Низька кваліфікація зварника Невідповідність хімічного складу присадного дроту до метала основи Помилки в виборі режиму зварювання “Це важливо”
Слайд 6Контроль: шаблон універсальний Параметри Визначення Діапазон контролю глубини раковин на поверхні труби, мм 0 – 15 Діапазон контролю глубини вибоїн на торці труби, мм 0 – 15 Діапазон контролю кутів скосу кромок труб, град. 0 – 45 Діапазон контролю величини притуплення, мм 0 – 50 Діапазон контролю величини зазору, мм 0 – 4 Контроль перевищення кромок при збиранні, мм 0 – 15 Контрольовані визначення діаметрів зварної проволоки, мм 1,0; 1,2; 2,0; 2,5; 3,0; 3,25; 4,0; 5,0 Діапазон контролю глубини розділення стику до корінного шару, мм 0 – 5 Діапазон контролю перевищення кромок післе зварки, мм 0 – 15 Діапазон контролю ширини зварного шва, мм 0 – 50 Діапазон контролю висоти підсилення зварного шва, мм 0 – 5 Габаритні розміри, мм 127х45х10 Вага, кг 0,15
Слайд 7“Загальний вигляд”
Слайд 8Дефекти у зварних з'єднаннях утворюються з різних причин. Так, нерівномірність перетину швів при дуговому і газовому зварюванні пояснюється порушенням режиму зварювання, підрізування – великим струмом і великою потужністю зварювального пальника, утворення пор у зварних швах – насиченістю їх воднем, азотом та іншими газами, тріщин – застосуванням сталей з підвищеним вмістом вуглецю або легуючих домішок, сірки і фосфору, непроварів – мала величина струму або недостатня потужність пальника, погане зачищення кромок тощо. Основними видами контролю якості зварних з'єднань є: випробування зварних швів на щільність (гідравлічні, пневматичні, часова проба), механічні випробування металу шва і зварних з'єднань (границя міцності, текучості, пластичність, статичний згин, ударна в'язкість), металографічні дослідження (макроскопічний і мікроструктурний аналізи зварних швів), просвічування швів рентгенівськими і гама-променями, ультразвуковий і магнітний методи контролю.
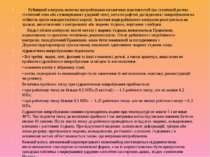
Слайд 9Руйнівний контроль включає випробування механічних властивостей (на статичний розтяг, статичний згин або сплющування і ударний згин), металографічні дослідження і випробування на стійкість проти міжкристалітної корозії. Зазначені види руйнівного контролю реалізуються на зразках, виготовлених з контрольних або зварних з'єднань, вирізаних з вибірки. Види і обсяги контролю якості металу і зварних з'єднань визначаються Правилами, нормативною та проектно-технічною документацією. Обсяг руйнівного і неруйнівного контролю, передбачений Правилами, може бути зменшений за погодженням з Держнаглядохоронпраці при масовому виконанні однотипних зварних з'єднань тощо. гідравлічним випробуванням підлягають: • Всі трубні, зварні, литі, фасонні та інші елементи і деталі, а також арматура, якщо вони не пройшли гідравлічного випробування за місцем їх виготовлення; • елементи котлів у зібраному стані; • котли, перегрівачі та економайзери після закінчення їх виготовлення, монтажу, реконструкцій чи ремонту. Величина пробного тиску при гідравлічному випробуванні приймається: • при робочому тиску не більше 0,5 МПа (5 кгс/см2) — 1,5 робочого тиску, але не менше 0,2 МПа; • при робочому тиску більше 0,5 МПа — 1,25 робочого тиску, але не менше робочого тиску + 0,3 МПа. Гідравлічне випробування повинно проводитись водою при температурі не нижче 5 i не вище 40°С. Час підняття тиску до величини пробного і час витримки котла під тиском повинен бути не менше 10 хвилин. Після зняття тиску до робочого проводиться огляд всіх зварних, вальцьованих, клепаних і роз'ємних з'єднань. При відсутності видимих залишкових деформацій, тріщин або ознак розриву, протікання в зварних, вальцьованих, роз'ємних i клепаних з'єднаннях і в основному металі об'єкт вважається таким, що витримав випробування. Кожний котел, автономний пароперегрівач і економайзер постачаються підприємством-виготовлювачем з паспортом встановленої форми, а на їx корпусі повинна бути прикріплена заводська табличка з маркуванням ударним способом паспортних даних, згідно з вимогами Правил.
Зварник повинен забезпечити високі технічні і експлуатаційні властивості виробів,що можливе тільки за умови точного виконання послідовності технологічних процесів і забезпечень їх стабільності. При правильній організації технологічного процесу контроль повинен бути його невід’ємною частиною. Висновок
Комментариев нет:
Отправить комментарий